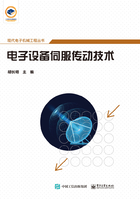
2.5.1 全数字机电伺服控制系统分布式、模块化硬件架构
全数字机电伺服控制系统根据其分布状况,可以分为集中模块化数字控制系统和分布式数字控制系统。集中模块化数字控制系统采用接口丰富的微控制器、可编程逻辑控制器和工业控制机等构成集中控制模块,具有易于对全局情况进行控制、计算和判断,易于统一协调安排等优点。分布式数字控制系统适应现代工业控制系统多元化、分散化的趋势,以微控制器、可编程逻辑控制器、工业控制机等数字控制器为基础,通过网络通信和现场总线,实现“集中管理、分散控制”,逐渐成为现代机电伺服控制系统的主流。
总线形式的全数字机电伺服控制系统包括上位机、伺服控制器、电动机、总线等部分。上位机主要实现信号采集、电动机调度、伺服指令输出等功能,伺服控制器主要完成电动机的数字控制,总线则实现信号的传递功能。上位机和伺服控制器之间均通过总线进行通信。上位机和伺服控制器主要有微控制器、可编程逻辑控制器和工业控制机。总线包括基金会现场总线、Lonworks、Profibus、HART、CAN总线、EtherCAT等。CAN总线形式的全数字机电伺服控制系统结构框图如图2-43所示。

图2-43 CAN总线形式的全数字机电伺服控制系统结构框图
1. 微控制器
微控制器(Micro Controller Unit,MCU)又称单片微型计算机或单片机,是把微型处理器和一定容量的存储器及部分输入/输出接口电路都集成在一块芯片上所形成的单芯片式微型计算机。常用的微控制器包括单片机、DSP等。
1)MCU的硬件组成
MCU的硬件主要包括中央处理器(CPU)、存储器(RAM/ROM)、总线和输入/输出接口(I/O)四部分,如图2-44所示。

图2-44 MCU的硬件组成框图
(1)中央处理器(CPU)。CPU是MCU的核心处理单元,它对系统产生的一切数据进行算术运算、逻辑运算和控制操作,主要由算术逻辑单元、寄存器组和控制器组成。算术逻辑单元用来执行基本的算术和逻辑运算;寄存器组用来存放操作数、中间运算结果及运算状态标志位等;控制器指挥整个系统的工作,按照一定的顺序从存储器中读取指令、译码,并在时钟信号的控制下发出操作指令,控制CPU及整个系统有条不紊地工作。
(2)存储器(RAM/ROM)。存储器的主要功能是存放程序和数据。存储器由寄存器组成,可以看成一个寄存器堆。存储器被划分成许多存储单元,每个存储单元有一个固定的单元地址,存储器内部自带地址译码器。访问存储器时,先由地址译码器将送来的单位地址进行译码,找到相应的存储单元;再根据送来的读/写命令确定访问存储器的方式,由读/写控制电路进行读出或写入操作。存储器主要包括随机访问存储器(RAM)和只读存储器(ROM)。
(3)总线。总线是计算机把各个部分有机连接起来的一组导线,是各个部分之间进行信息交换的公共通道。MCU中将把CPU、存储器和I/O接口连接起来并相互传送信息的信号线和控制线统称为系统总线,包括地址总线、数据总线和控制总线。
(4)I/O接口。外部设备与计算机之间通过I/O接口连接。I/O接口包括数字I/O接口和ADC模拟量I/O接口。数字I/O接口内部电路含端口锁存器、输出驱动器和输入缓冲器等电路,通常具有复用功能;ADC模拟量I/O接口需要经过A/D或D/A转换电路转换为数字信号后再输入/输出。
(5)外部设备。外部设备是输入、输出设备的统称,是计算机系统的重要组成部分,起到信息传输、转入和存储的作用。常见输入设备包括模/数转换器等,常见的输出设备包括数/模转换器等。
2)MCU的功能特点
MCU是一个集成了CPU、RAM、ROM、I/O等的微型计算机,可以按照用户编写的程序执行相应的控制功能,既可以用于简单的开关控制、定时调节、电动机驱动等,又可以用于更加复杂的机电系统控制。MCU特点明显,具体包括:①集成度高、体积小;②可靠性高,抗干扰能力强;③控制功能强;④可扩展性好;⑤功耗低;⑥性价比高。
3)MCU的应用场合
单片机具有体积小、功耗低、控制功能强、环境适应能力强、扩展灵活和使用方便等优点,广泛应用于智能仪器仪表(如功率计和示波器等各种分析仪器)、工业控制(如工厂流水线的智能化管理、电梯智能化控制、各种报警系统等)、家用电器(如洗衣机、电冰箱、空调机等)、办公用品(如打印机、传真机等)、网络通信(如楼宇自动通信呼叫系统、列车无线通信、移动电话、无线电对讲机等)、医疗设备(如医用呼吸机、监护仪、超声诊断设备等)、汽车电子(如发动机控制器、GPS导航系统、制动系统等)、军用武器设备(如导弹、雷达等)中。
2. 可编程逻辑控制器及其模块化设计
可编程逻辑控制器(Programmable Logic Controller,PLC)是一种面向工业自动化应用的数字运算操作电子系统,它在可编程存储器内部执行可存储的逻辑运算、算术运算、计数及定时等操作,通过数字式或模拟式的输入、输出来程序化控制各种类型的机械设备或生产过程。
1)PLC的硬件组成
PLC的品牌众多,所采用的指令系统与编程语言也不尽相同,但结构组成却大致一样,主要由CPU模块、输入模块、输出模块、编程装置和电源等相对标准化的模块组成,如图2-45所示。下面分别介绍各个组成部分。

图2-45 PLC的硬件组成框图
(1)CPU模块。在PLC控制系统中,CPU模块相当于人的大脑,主要作用是采集输入信号、执行程序处理、输出操作信号。CPU模块主要由CPU芯片和存储器组成。
CPU芯片负责输入/输出处理、程序解算、通信处理等,是PLC硬件的核心。PLC的主要性能,如速度、规模都由CPU的性能决定。一般PLC使用的CPU芯片包括三类:通用微处理器、单片微处理器和位片式微处理器。其中8位和16位通用微处理器或单片微处理器常分别用于小型和中型PLC,而高速位片式微处理器多用于大型PLC。
存储器分为系统程序存储器和用户程序存储器。前者主要用来存放PLC的系统软件固有程序,后者主要用来存放I/O状态及用户程序。一般PLC使用的物理存储器包括三类:随机存取存储器(RAM)、只读存储器(ROM)、可电擦除可编程的只读存储器(EPROM)。
(2)I/O模块。输入模块用来接收和采集用户及生产过程的输入信号。数字量输入模块用来接收从各类按钮和开关传送来的数字量电平输入信号;模拟量输入模块用来接收电位器、测速发电机、编码器等传感器提供的连续变化的模拟电流、电压信号。
输出模块用来送出程序计算结果,对输出信号进行功率放大,驱动执行元件实现设备控制。数字量输出模块用来控制指示装置,如电磁开关、指示灯、数字显示装置等;模拟量输出模块用来控制执行装置,如调速阀、变频器等。
(3)编程装置。编程装置用来生成用户程序,并对它进行编辑、检查和修改。手持式编程器不能直接输入和编辑梯形图,只能输入和编辑指令表程序,因此又称为指令编程器。它的体积小、价格便宜,一般用来给小型PLC编程,或用于现场调试维修。
(4)电源模块。PLC常用电源为220V AC或24V DC。内部的开关电源为各模块提供5V、、12V等多种直流电源。小型PLC的输入电路、传感器、驱动负载等通常使用由用户提供的24V直流电源。
2)PLC的功能特点
由于具有很高的性价比,目前PLC技术广泛应用于各个工业领域。PLC不仅能够实现数字量的逻辑控制,如代替继电器进行组合逻辑控制、定时控制与顺序逻辑控制等,还能够用于各种智能控制设备的数据通信与各类执行机构的联合运动控制。PLC的特点可归结为:①编程简单,方法易学;②功能强大,性价比高;③配套齐全,通用性强,使用方便;④可靠性高,抗干扰性强;⑤设计施工的工作量大幅减少;⑥体积小,能耗低。
3)PLC的应用场合
PLC在国内外广泛应用于钢铁、石油化工、机械制造、汽车装配、电力、轻纺、电子电气等各行各业,其具体应用包括以下几个方面:①开关量的逻辑控制;②模拟量控制;③运动控制,PLC具有专门的运动控制模块,如可驱动步进电动机或伺服电动机的单轴或多轴位置控制模块,可以用于圆周运动或直线运动的控制,在各种机械、机床、机器人、电梯等场合有广泛的应用;④过程控制;⑤数据处理;⑥通信及联网。
3. 工业控制机及其模块化设计
工业控制机(Industrial Personal Computer,IPC)是一种加固的增强型个人计算机,它以模块化设计理念为基础,采用某种标准总线作为通信设计,集成符合工业标准的主板、符合工况要求的功能模块和多种I/O模块,从而实现用户对设备的功能需求。在各类工业领域,IPC能够稳定且可靠地运行。
1)IPC的硬件组成
为了提高通用性、灵活性和扩展性,方便用户使用,IPC的各部件均采用模块化结构设计。在设备底板上,它采用一条并行总线,能够插接多个不同的功能模块。IPC的硬件组成框图如图2-46所示,包括构成计算机基本系统的主板、人机外设、系统支持板、磁盘系统,以及上百种工业I/O接口板。在内部总线作用下,各模块实现信息互通,并由CPU直接完成数据的传输和处理。下面具体介绍IPC的硬件组成部分。

图2-46 IPC的硬件组成框图
(1)并行总线:并行总线由内部总线和外部总线构成。前者是IPC内部各模块进行信息传送的公共通道,常用的国际标准有PC总线、VME总线、STD总线和MULTIBUS总线等;后者是IPC与外部设备实现功能通信的公共通道,常用的国际标准有RS-232C、RS-485和IEEE-488通信总线等。
(2)主板:由中央处理器(CPU)、内存储器(RAM、ROM)等部件组成,它是IPC的运算及处理核心。
(3)人机外设:是用户与计算机交流通信的输入和输出设备,如键盘、鼠标、显示器、打印机等。
(4)系统支持板:主要功能包括系统程序运行监视、电源断电保护、工作定时及记录日志等。具体来说,就是系统能够自主监测设备运行环境,当系统环境异常时(如存储崩溃、程序错误、死机断电),系统能够及时检测并保护已有的重要数据和寄存器状态,同时自动记录操作和状态日志供用户查看分析,并进入保护模式使设备恢复运行。
(5)磁盘系统:包括通用的软盘、硬盘系统,也能与外部移动磁盘进行读/写操作。
(6)通信接口:是IPC与外部智能设备的通信接口,常用的接口通信协议有RS-232C、RS-485和IEEE-488等标准。
(7)输入/输出模块:是IPC在生产过程中实现外部和内部信号传递及转换的模块,主要包括模拟量输入(AI或A/D)和输出模块(AO或D/A)、数字量输入(DI)和输出模块(DO)等种类。由于输入或输出均涉及生产现场被控参数的种类、数量、精度等,因而该模块是IPC硬件中性能差异最大、品种类型最多、用户选择最多样的组件。
2)IPC的功能特点
IPC是一种专用于工业场合下的控制计算机。一方面,工业环境常常处于高温、高湿、腐蚀、振动、冲击、灰尘,以及电磁干扰严重、供电条件不良等恶劣环境中;另一方面,工业生产的过程和工艺要求因行业、原料、产品的不同而不同。IPC采用的总线技术、模块化结构和多重抗干扰措施,使IPC具有其他计算机无法比拟的功能特点。IPC的优点可归纳为:①可靠性和可修复性好;②环境适应性强;③通用性和扩展性好;④软件丰富、功能强大;⑤控制实时性强。
3)IPC的应用场合
总线式IPC具有可靠性、实时性、扩充性、兼容性等诸多优点,能满足不同层次、不同控制对象的需要,能在恶劣的工业环境中可靠地运行。随着自动化水平的提升,IPC广泛应用于各种控制场合,具体如下:①医疗行业,如监护仪、诊断仪等;②交通行业,如车载野外仪器设备、超速抓拍系统等;③服务行业,如校园一卡通等;④资源监测行业,如污水处理系统等;⑤设备与机械制造行业,如自动配料控制系统等;⑥钢铁自动化行业,如钢厂能源调度系统等;⑦电力自动化行业,如电力调度系统等;⑧通信设备行业,如光缆监测控制系统、计费系统等;⑨楼宇自动化行业,如智能家居系统等;⑩机器视觉行业,如在线读码系统等。
4. 分布式数字控制系统及现场总线技术
分布式数字控制系统包括集散控制系统(Distributed Control System,DCS)和现场总线控制系统(Fieldbus Control System,FCS),两者均采用管理与控制相分离的系统方式,其核心思想为“集中管理、分散控制”。DCS采用层次化的体系结构,利用上位机实现集中监视管理,同时将若干下位机分散到工控现场进行分布式控制,信息传递局限在上、下位机之间;FCS用现场总线这一开放的、可互操作的网络将现场各控制器及仪表设备连接起来,实现一对N连接,从底层的传感器、变送器和执行器到最高层的操作站,全都可以双向通信,同时控制功能彻底下放到现场,真正实现了“集中管理、分散控制”。DCS和FCS的结构对比如图2-47所示。

图2-47 DCS和FCS的结构对比
FCS具有以下特点:①功能更加分散,可以由现场仪表组成自治的控制回路,现场设备具有足够的自主性;②具有良好的抗干扰能力,大大提高了控制系统的可靠性;③采用彻底分散的分布式结构,一方面大量节省了布线费用,另一方面也便于系统的安装、调试和维护,降低系统的安装维护成本;④具有开放性的特点,能够保证良好的互换性和互操作性。
FCS得到快速的发展,最重要的因素在于现场总线技术的应用。目前,有多种现场总线技术具有较大的影响力,获得广泛的应用,包括基金会现场总线、Lonworks、Profibus、HART、CAN-bus、EtherCAT等。
1)基金会现场总线(Foundation Fieldbus,FF)
FF是由现场总线基金会推出的一种现场总线。它提供了两种物理层标准,分别为H1和H2。其中H1是一种低速总线,传输速率可达31.25Kbps,传输距离为200m、450m、1200m、1900m四种,主要用于过程控制和总线供电,支持本质安全设备和非本质安全总线设备。H2是高速总线,传输速率为1Mbps(距离750m)或2.5Mbps(距离500m)。H1和H2可以通过网桥实现通信连接,每段节点数可达32个,并可使用中继器扩展节点,最多可达240个。FF总线在设备互操作性的提高、过程数据的改善、系统安全性和可靠性维护及预测等方面有明显的优点。
2)Lonworks
Lonworks是采用ISO/OSI模型的现场总线,由美国Echelon公司于20世纪90年代初推出。它具有7层通信协议,并提供全部总线服务。该总线以神经元芯片作为核心,控制网络中各个节点内置的神经元芯片来进行事件处理,并完成协议的监控功能。该总线按照统一通信协议方式,在不同介质作用下将处理结果发送给网络中的其他节点。一个Lonworks网络可以拥有较多节点,一般在几个到几千个之间。Lonworks能够提高系统的稳定性和响应速度,并降低系统的维护、运行等费用。
3)Profibus
Profibus是德国Siemens公司提出并大力推广的现场总线,技术非常成熟,目前为德国国家标准DIN19245和欧洲标准EN50170,在工程上的应用十分广泛。Profibus包含三个系列总线,分别为Profibus-PA、Profibus-DP和Profibus-FMS。Profibus-PA用于过程自动化的低速数据传输,其基本特性与FF的H1总线相同,可以提供总线供电和本质安全。Profibus-DP与Profibus-PA兼容,基本特性与FF的H2总线相同,可实现高速传输,适用于分散的外部设备和自控设备之间的高速数据传输,用于连接Profibus-PA和实现加工自动化。Profibus-FMS适用于一般自动化中的中速数据传输,主要用于纺织电气传动、速度传感器、工控执行器等。
4)HART
HART是美国Rosemount公司开发并逐渐推广使用的现场总线,其特点是在现有模拟信号传输线上实现数字信号通信,属于模拟系统向数字系统转变过程中的过渡性产品。HART通信模型由物理层、数据链路层和应用层组成,采用统一的设备描述语言DDL,由HART基金会登记管理这些设备。HART能利用总线供电,可满足本质安全防爆要求。
5)CAN-bus
CAN-bus是由德国BOSCH公司开发的控制器局域网,作为国际标准ISO11898而应用最为广泛。该总线采用多主机竞争式串行通信,即通信网络中各节点根据访问优先级采用逐位仲裁竞争方式向总线其他节点发送数据通信请求,不分主次地进行实时自由通信。CAN-bus传输介质可以采用同轴电缆,在10km的远距离通信情况下仍可保持约5Kbps的高速数据传输。CAN-bus总线技术较为先进,性价比较高,在目前的汽车电子、安防监控、智能制造等工业控制领域具有强劲的竞争力。
6)EtherCAT
EtherCAT是以以太网为基础的现场总线系统,最早由德国Beckhoff公司研发。EtherCAT充分利用了以太网技术的全双工传输特性,它使用主从模式进行访问控制,通信由主站发起,主站发出的数据帧传输到一个从站站点时,从站将解析数据帧,每个从站从对应报文中读取输出数据,并将输入数据嵌入子报文中,同时修改工作计数器WKC的值,以标识从站已处理该报文。网段末端的从站处理完报文后,将报文转发回主站,主站捕获返回的报文并对其进行处理,完成一次通信过程。一个通信周期中,报文传输延时大概为几纳秒。EtherCAT可以支持线形、树形和星形设备连接拓扑结构,物理介质可以选100Base-TX标准以太网电缆或光缆,使用100Base-TX电缆时站间间距可以达到100m。EtherCAT克服了传统以太网先对数据包进行解析,再复制成过程数据而造成通信效率低的缺陷,并为系统的实时性能和拓扑的灵活性树立了新的标准,同时还具有高精度设备同步、降低现场总线成本等特点。EtherCAT在包装机、高速印刷机、注塑机、木工机械等场合得到了广泛应用。