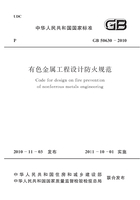
4.5 火法冶金
火法冶金是提取并提纯有色金属的常用方法,其冶金方法有熔炼(造锍熔炼)、吹炼(锍的吹炼)和火法精炼。选用的冶金炉主要有:反射炉、电炉、鼓风炉、闪速炉、艾萨炉、奥斯麦特炉、回转精炼炉等,产出成品为粗金属(为铜、镍等常用的冶金工艺)。此外,还可通过还原熔炼、挥发还原熔炼等方法,生产各类有色金属的半成品或成品(为其他多种金属常采用的冶金工艺);火法精炼则是许多品种粗金属的进一步冶炼提纯。另外,火法冶金工艺系统还应包括冶炼前(后)处理或称做冶金物料准备(炼前准备等),通常包括:精矿解冻、配料、干燥、制粒(压团)以及煅烧、焙烧、烧结等多种冶金工艺类型或分支。
4.5.1 冶金生产的各类炉窑(反应装置)当使用煤粉时,其防火设计应符合下列规定:
1 仓式泵、煤粉储罐、喷吹罐等压力容器设计应符合现行国家标准《钢制压力容器》GB 150的有关规定;
2 当喷吹烟煤及混合煤粉时,应在喷吹系统的关键部位设置温度、压力和一氧化碳浓度、氧浓度等的监控、报警装置;
3 当喷吹烟煤及混合煤粉时,仓式泵、煤粉储罐、喷吹罐等容器的加压和流化介质应采用惰化气体;
4 煤粉输送和喷吹系统中的充压、流化、喷吹等供气管道均应设置逆止阀;
5 当用压缩空气作为煤粉输送和喷吹的载送介质时,在紧急情况下应能立即转化为氮气的惰化措施;
6 煤粉仓的仓体结构应能使煤粉顺畅自流,当喷煤系统停止喷吹且需要及时排出时,有利于煤粉排空;
7 厂房应作好通风设计,宜采用开敞式建筑。室内装修应简洁,应有避免粉尘积聚的措施;
8 当采用直吹式制粉系统时,尚应符合本规范第4.11节的有关规定。
煤粉在各类冶炼生产中,既作为燃料有时还兼做还原剂,在冶金生产中广泛地使用,其防火、防爆设计十分重要。
2 烟煤、混合煤粉喷吹易发生燃爆事故,必须设置监控、报警及联锁安全装置,以及自动充入保护性气体等设施;对于其他类型煤粉依据其特性,设置相应的安全监控装置;
3 采用烟煤、混合煤粉喷吹时易发生燃爆事故,故在其加压和流化中,介质应采用惰化气体。此款依据现行国家标准《高炉喷吹烟煤系统防爆安全规程》GB 16543中的有关规定制定的;
4 为了防止出现煤粉倒流,引发燃爆和其他不安全问题,确保生产正常,应在供气管道上设置逆止阀装置;
5 现行国家标准《高炉喷吹烟煤系统防爆安全规程》GB 16543和国家电力行业标准《火力发电厂煤和制粉系统防爆设计技术规程》DL/T 5203—2005以及煤炭部行业标准《煤粉生产防爆安全技术规范》MT/T 714—1997等规程、规范中都明确规定:当采用压缩空气作为喷吹输送介质时,应采用氮气或惰化气体作为保护性气体,且规定对选用惰化气体作保安气源时,应有防止泄漏的安全措施。
本规范从有色行业多年生产实践和确保安全出发,规定当用压缩空气作为煤粉输送及喷吹的载送介质时,紧急情况能立即转化惰化气体保护要求。惰化气体应选用氮气或其他惰性气体,此规定对于多数有色金属工程项目是可以做到的。但据调查,某些有色金属企业具有使用蒸汽作为应急防护的经验,并已经有多年的安全运行实践。对此也可以选用蒸汽应急,但是会给善后清理恢复工作带来较多的麻烦;
6 煤粉仓体内壁应平整光滑,下料锥体壁与水平夹角不小于70°,便于煤粉顺畅自流。当喷吹系统停止工作后,为了避免煤粉长时间在仓内存置引起自燃或爆炸,应以惰性气体有效地保护,减小助燃的条件。当需要在一定的时间内将仓内剩余的煤粉及时排空,仓体结构应有利于煤粉方便地排出;
7 根据现行国家标准《高炉喷吹烟煤系统防爆安全规程》GB 16543、国家电力行业标准《火力发电厂煤和制粉系统防爆设计技术规程》DL/T 5203—2005以及原煤炭工业部行业标准《煤粉生产防爆安全技术规范》MT/T 714—1997中的相关要求制定。
4.5.2 冶金生产的各类炉窑(反应装置),当使用燃气时,其防火设计应符合下列规定:
1 煤气使用装置的防火设计应符合现行国家标准《工业企业煤气安全规程》GB 6222、《城镇燃气设计规范》GB 50028的有关规定;液化石油气、天然气使用装置的防火设计应符合现行国家标准《石油天然气工程设计防火规范》GB 50183的有关规定;
2 当炉窑的燃烧装置采用强制送风的烧嘴时,在空气管道上应设置泄爆阀;
3 使用燃气的炉窑点火器,应设置火焰监测装置;
4 在可燃气体使用区域的适当位置,应设置可燃气体浓度监测、报警和相应的机械通风装置;
5 燃气管道进入厂房之前适当位置处,应设置切断总管的阀门;厂房内的燃气管道应架空敷设;
6 连铸工序用于切割的乙炔、煤气、液化石油气以及氧气的管道上,应设置紧急切断阀。
各类燃气是有色金属冶炼生产中重要的工艺条件,是生产过程中不可或缺的燃、原料。随着高效、节能、环保的迫切要求,燃气的应用会更为广泛,必须做好防火设计。
4 在车间内设置可燃气体监测报警和机械排风装置时,其所在的位置,应视被检测气体与空气的密度大小不同,或设置在车间的下部(散发的燃气密度较空气大时),或设置在车间的上部(散发的燃气密度较空气小时)相应的敏感区位,才能有效地检测并及时排除火情的隐患。
4.5.3 冶金生产的各类炉窑(反应装置),当使用燃油时,其防火设计应符合下列规定:
1 车间供油站宜靠外墙设置,应采用不燃烧体隔墙和不燃烧体楼板(屋顶)与厂房分隔,并应符合本规范第6.2.4条的有关规定;
2 车间供油站的储存油量,应以该车间2d的需求量为限,并应符合下列规定:
1)甲类油品不应大于0.1m3;
2)乙类油品不应大于2.0m3;
3)丙类油品不宜大于10.0m3。
3 油罐内的油品加热宜选用罐底管式加热器,油品的加热温度应控制在油品闪点温度以下不小于10℃;
4 输送燃油的管路应设置快速切断阀门;
5 燃油储存、输送设备及管道应有防雷、防静电设施,设备及管道的保温层应采用不燃烧材料;
6 室内油泵间应设置机械通风装置(防爆型),通风换气量应根据:地上布置不少于7次/h、地下布置不少于10次/h的换气次数,经计算确定。
冶金生产的各类炉窑(反应装置)在使用燃油时强调以下有关要求:
1 有色金属生产中使用的液体燃料多为重油或渣油,特殊情况可能使用原油或柴油,主要用于工业炉、窑等的点火、加热、还原使用。由于我国多为石蜡基石油,含蜡高黏度大、凝固点较低,重油(或渣油)在室温下一般流动性较差,多数呈凝固状态,故在卸油、输送及使用中均需加热,提高其流动性和雾化性。为保证车间供油的顺畅,满足生产的急需,通常在主要用油车间附近或主厂房内建立车间供油站。该站目的是生产的应急供油,不需要也不允许设置较多的贮、卸燃油装置及设施。另按防火分隔设计要求,车间供油间应与其他区域以实体墙及楼板隔开;
2 车间供油站系保证重要炉、窑日常生产用油的需求而设置的,由于环境和安全等原因,在保证生产基本需要的前提下,应限制储存的油量不能过多,尤其易燃易爆的甲、乙类油品危险性大,限制更是十分必要的。通常以满足24h用量较符合生产调配的安排,但其储存量绝对值也不允许过大。参照现行国家标准《石油库设计规范》GB 50074中第10.0.1条车间供油站的规定,并结合有色金属生产的特点和管理经验,一般限制为:以该车间2d用油量为限,且:甲类油品应小于0.1m3,乙类油品应小于等于2.0m3。对于丙类油品基于相对较安全(使用重油、渣油闪点>60℃),且生产的需求量相对较大,经行业内多年使用经验证实,采用严格管理制度并加强监控力度,丙类油品的存储量10m3是合理且安全的。根据统计,目前有色工业炉、窑2d内最大用油量多数在10m3上下,基本满足正常生产的需要。故本规范规定车间供油站丙类存油量限定为:重油、柴油(闪点≥60℃)不宜大于10m3;
3 为了便于输送并提高油品的燃烧效率,油罐内的油需要加热,达到一定的温度。但温度不能过高,不允许高于或接近油品闪点温度。如果罐内重油(原油)需要脱水,其加热温度也不能超过水的沸点温度,不然会发生“冒罐”事故。此外,考虑我国重油的质量特性,一般在使用前还需要通过加热器进行二次加热,故储油罐内一般加热到适当的温度即可。
4.5.4 冶金物料准备(含干燥、煅烧、焙烧、烧结等类型)生产工艺的防火设计应符合下列规定:
1 炉窑及其排烟、收尘系统应设置封闭的隔热层,其密封性能、外表面温度等均应符合现行国家标准《工业炉窑保温技术通则》GB/T 16618的有关规定;
2 输送热物料时,应选用与之温度相匹配且由难燃烧或不燃烧材料制作的装置;
3 烧结机点火器应设置空气、煤气低压报警装置和指示信号以及煤气低压自动切断的装置;
4 烧结机点火器烧嘴的空气支管应采取防爆措施,煤气管道应设置紧急事故快速切断阀;
5 炉窑主抽风系统出口电除尘器,应根据烟气和粉尘性质设置防爆和降温装置;
6 输送可燃介质的管道不宜通过高温、明火作业区的上方,必须通过时应采取安全防护措施;
7 对于具有间歇性操作的炉窑,应有防止发生燃烧爆炸事故的技术措施。
冶金物料准备包括:干燥、煅烧、焙烧、烧结等工艺类型分支(子系统),它是火法冶金系统中的重要分支。与冶炼工艺的区别在于炉体内物料尚未达到完全熔化的状态,炉体内尚不会形成熔融体。冶金物料准备又以其不同的目标,细分为:干燥,即原、辅材料的物理脱水过程。一般采用燃烧重油(煤粉、煤气、天然气)加热,使物料在400℃以下温度的环境下,脱水后达到干燥要求;煅烧,比干燥需要更高的温度,不仅脱去介质的附着水,而且要去除其化学结合水。工作温度一般在600℃以上(有的则高达1000℃左右),加热分解氢氧化物、硫酸盐、碳酸盐等;焙烧,是为了提供适应下道冶炼工序需求的化学组分,进行的加热处理工艺过程。以煤气、天然气或重油为热源,以较严格温度控制(低于介质的熔化温度),或使物料实现部分或全部脱硫,或确保生成硫酸盐,或满足还原剂的需要等,一般工作温度在600℃~1000℃;烧结,系对硫化精矿既达到脱硫,又获得一定机械强度、孔隙度的块状物料的工艺过程。以煤气或焦粉为燃料,一般工作温度800℃~1000℃。冶金物料准备的防火要求主要是:
1 炉窑、燃烧室的隔热、密封性能、外表面温度等设计标准,均应符合现行国家标准《工业炉窑保温技术通则》GB/T 16618的有关规定,避免高温散发、烟气泄漏存在隐患;
2 干燥、煅烧及烧结生产中有时会因操作不正常,出现部分高温、异常的炉料或烧结块,可能会导致输送设施毁坏、燃烧或加剧设施老化等事故,设计应有可靠措施加以防止;
3、4、5 三款的规定依据现行国家标准《钢铁冶金企业设计防火规范》GB 50414“烧结和球团”中的有关要求制定,烧结机需要24h不间断地使用燃气,是火灾的高危区,防火设计较严格。烧结工艺在钢铁领域内成熟且先进,使用经验和技术标准都值得肯定,故参考其标准的要求制定出本规范的规定,对于有色金属烧结工艺以及相关炉窑的点火装置、除尘等设施防火设计会具有一定的借鉴意义;
7 在干燥、煅烧、焙烧、烧结窑等炉窑生产中,间断作业时会发生燃烧室一氧化碳的聚集,从而引发燃爆事故,在工程设计和运行中应有预防的技术措施。
4.5.5 冶炼(含熔炼、吹炼、精炼等类型)生产工艺的防火设计应符合下列规定:
1 冶炼炉及其排烟、热回收系统的外壳及其隔热层,其密封性能、外表面温度等应符合现行国家标准《工业炉窑保温技术通则》GB/T 16618的有关规定;
2 冶炼生产工艺使用氧气时,其防火要求除应符合现行国家标准《氧气及相关气体安全技术规程》GB 16912的有关规定外,尚应符合下列的规定:
1)炉窑前使用的氧气管道应严格脱脂清理;
2)氧枪的氧气阀站及由阀站至氧枪软管的氧气管线,应采用不锈钢管;当难以避免而采用碳素钢管时,应在连接软管之前加设阻火铜管;
3)使用氧气的在线仪表控制室和氧气化验等场所,应设置氧浓度监测和富氧报警装置;
3 当炉窑装置使用氢气时,其防火设计应符合本规范第4.6.1条、第4.8.6条的有关规定;
4 当炉窑装置产生(逸出)一氧化碳、煤气时,应设置相应的收集处理装置;其防火安全设计应符合本规范第4.5.2条的有关规定;
5 使用或产生易燃、易爆金属(非金属)粉料(尘)时,其防火安全设计应符合本规范第4.6.1条的有关规定;
6 冶炼炉及其配套设施的密闭冷却水系统,应设置温度、压力、流量等检测以及事故报警信号和联锁控制装置,并宜独立设置循环水系统和应急供水装置;
7 冶炼(喷吹)炉应在工程设计(含生产操作)中采取防止泡沫渣溢出事故的技术措施;对冶炼(喷吹)炉的控制(操作、值班)室和炉体周围设施,应采取有效的安全防范措施,并应符合本规范第4.5.6条、第6.2.2条的有关规定;
8 根据工艺配置要求,在冶炼炉熔体放出口邻近区位处,当设置容纳漏淌熔体的应急事故坑时,事故坑距离厂房结构柱的净距不应小于0.5m,邻近事故坑的厂房钢结构柱应按本规范附录A的有关规定,进行耐火稳定性的验算和耐火防护;
9 用于吊运熔融体或进行浇铸作业的厂房起重机(吊车)应采用冶金专用的铸造桥式起重机;
10 各类冶炼炉(窑)的控制(操作、值班)室应避开加料、排料(渣)等炽热、喷溅区域,控制(操作、值班)室应采取防火安全措施,其出口应设在安全区位内,并应符合本规范第6.2.2条的有关规定;
11 运输熔融体物料(含金属或炉渣)装置出入厂房,应采用专用的铁路运输线;如采用无轨运输时,应设置安全专用通道;
12 在铜锍、镍锍等熔融介质水淬池的两侧,应设置混凝土的防爆(防火)墙;
13 在使用或产生易燃、易爆介质、粉末(尘)的区域内,相关装置及管道应有导除静电的有效措施,楼、地面应采用不发生火花的面层;
14 对部分有色金属冶炼(钛、锂等)生产工艺及其使用介质,遇水会发生燃烧或次生灾害的厂房(场所),不应设置消火栓,也不宜设置冲洗用水装置,禁止地面积水。
冶炼生产工艺包括造锍熔炼、吹炼、还原熔炼、还原挥发熔炼以及火法精炼等,是属于具有熔池类工业炉(窑)的冶炼系统。其中造铳熔炼是重金属(铜、镍、钴等)的主要熔炼方法,系对硫化精矿进行氧化反应,将炉料中的主要金属以硫化物形式富集成锍,使部分铁氧化造渣的工艺过程。采用传统冶炼手段以及新型的富氧强化冶炼工艺,以煤粉、油类、煤气、天然气、氧气作为主要或辅助燃料,工作温度均在1150℃以上;锍的吹炼系对锍(铜锍、镍锍)进行氧化脱硫、除铁等杂质,而对主金属继续富集的工艺过程,以空气或富氧鼓入熔体,发生强烈氧化反应,工作温度1150℃~1250℃;还原熔炼系利用相关类金属—铅、锡、锑、铋等对氧或硫的亲和力不同,在一定温度作用下,将主金属与杂质和脉石分离的工艺过程,通常以煤粉、焦炭、重油作还原剂和燃料,而钨、钼、钛、锆等高熔点金属矿还以H2、CO、Cl2或金属Mg作还原剂;还原挥发熔炼是利用主金属及其化合物的蒸汽压比较大的特性,通过金属蒸汽的逐步冷凝收集,使主金属与杂质和脉石分离或者提纯的工艺过程,如锌、汞、镉、镁等金属的提取和硅、锗、钛等氯化物的获得,均可采用还原挥发熔炼工艺。工作温度一般在1100℃~1700℃,使用的还原剂有焦炭、氯气、硅等,其挥发产物呈各种状态有熔融金属、结晶状固体、微细粉末等;火法精炼即是通过改变温度、压力、或添加新成分,从而形成新相(液、固、气等相),使主金属或杂质转移到新相中,从而实现分离提纯的工艺过程,火法精炼手段多种,如熔析、蒸馏、添加新金属、添加碱金属类,以及区域熔炼、定向结晶等方法,使用介质有压缩空气、氧气、重油、天然气、煤粉以及氢气、氯气等,工作温度依不同品种而异。火法冶炼工艺系统的基本特征是冶金炉具有一定的熔池空间(熔融体区),物料进入炉体后迅速熔化,呈熔融态并构成一定的液面;
2 近年来,冶炼过程中反应风的富氧浓度趋向不断增高,以氧气为代表的强化熔炼冶金技术,在节能、降耗、提高产能具有明显的优势。使用氧气(含富氧)等助燃气体时,防火安全不可忽视诸如氧气管道在安装就绪和使用前,必须彻底清除掉管道内的油脂、油渍等污物,否则会发生燃爆危险;氧枪的氧气阀站及由阀站至氧枪软管的氧气管线,宜选用不锈钢等避免出现火情隐患;
按现行国家标准《氧气及相关气体安全技术规程》GB 16912规定,对于工作场所氧浓度(体积比)报警的界限:缺氧为<18%,富氧为>23%,当某工作场所氧浓度>23%时,会成为浓郁的助燃空间环境,偶遇星火即可能酿成火海。在使用氧气的有关场所,必须防止局部的氧气积聚,应在相关区位设置监测及报警装置,有关要求应符合氧气安全标准的规定;
6 炉(窑)及其喷枪等相关设施的密闭冷却水系统,宜独立设置自成一体,应对冷却水温和水量差值等进行监测,并应设置事故报警信号及联锁控制装置。冷却水系统独立设置,有利于及时检查发现隐患,也便于快速应急处理,这对保证冶金炉的生产安全十分重要。通常在冶炼生产过程中,炉体会出现一些不利的因素,炉体、氧枪的水套及水冷管路可能出现渗漏。如果渗漏严重,就会发生重大火灾或爆炸事故。20世纪90年代中期,某有色金属企业由于冶金炉循环冷却水系统渗漏,引起炉内耐火砌体损坏,导致大量熔融体烧穿炉壳急剧外泄,引发一起重大火灾安全事故,造成严重的经济损失;
7 本款针对国内近年来浸没式喷吹熔炼炉连续出现数起泡沫渣溢出炉体,引发火灾伤害事故而加以总结制定的。在工艺生产中应通过科学配料选择合理的渣型,并对炉内的压力、液面等参数的变化设置监测、报警和联锁控制装置,就可能避免发生泡沫渣过量以至于溢出炉体的灾害。2007年9月9日,我国某有色冶炼厂富氧顶吹冶金炉,在试生产过程中发生了泡沫渣喷出炉体的重大火灾事故。在短暂的时间里,1100℃熔融体从炉体向外剧烈喷射。热浪方向性强冲击力极大,9.50m仪表室的装备及建筑全部被摧毁,甚至波及到47m以外的门窗。导致8人死亡10人受伤惨痛悲剧瞬间发生。
在“9·9”事故的调查中发现喷出的渣含Fe3O4占到27%之多(通常Fe3O4应限制在12%以下),此系泡沫渣发生的重要内因。而当炉内出现泡沫渣后,炉体的压力、液位发生变化,应当立即提升喷枪停止送风,迅速加入还原介质,是能够避免事态恶化的。但原有的联锁控制失效,又未能适时采取紧急措施,引发重大火灾伤害事故。为此,总结经验吸收教训,强调在工程中应设置可靠的监控、报警和连锁切换装置,同时应做好控制室及炉体周围的管线、设施和人员的安全防护设计;
8 依据多年生产和工程的经验,在某些类型有色冶金熔炼炉旁,工艺专业提出预先设置相关的事故坑(安全坑)技术要求。其目的在于:炉体自身操作意外或其他不测的应急之需,当冶炼炉生产中遇到难以控制的内、外部因素时,可使得大量熔融体(含锍、渣)从放出口外泄,并导入具有缓冲、接纳的设施——“事故坑”(安全坑)。以人为可控的措施与手段,避免引发火灾、爆炸事故的灾害发生。
同时为了防止泄漏炉料时高温对周围的厂房结构(柱等)的不利影响,应按本规范附录A进行耐火稳定性的验算,并根据评估、验算和实际需要对钢结构构件设置防火保护;
9 吊运及浇铸熔融体生产作业危险性大,是涉及安全生产的关键工序。在我国冶金(含钢铁、有色)行为内已先后出现过多起火灾安全事故,仅2007年一年中,即发生多起吊运钢包引发的重大火灾事故,死伤达数十人。其中某特殊钢公司,起重机在钢包吊运中发生滑落倾覆,致使熔体外溢,酿成一起死伤38人的重大火灾恶性事故(见本规范第4.5.6条说明)。众多钢包吊运的严重事故,究其原因一是选用吊运设备简陋或安全不达标,二是操作严重违规。因此,本规范强调起重机应采用可靠度高的冶金专用铸造或加料桥式起重机,在现行国家标准《起重机设计规范》GB 3811中对于用在吊运液态金属和危险品的起重机,规定了增设制动器、限制升降速度等特别要求。工程设计人员必须清楚认识:起重机是保证生产的基础性设施,严禁降低安全标准;
10 冶炼炉的控制(操作、值班)室应远离炉口喷溅和吊运熔体等作业区域,且宜少设或不设窗户。当难以避免时,应设置安全防护隔板;采用双层安全(加丝、钢化)玻璃;设置防喷溅的保护装置等。控制室的出入口应设在安全区位内,对于疏散难度大或建筑面积较大的控制室,应增加控制室的安全出口;
11 熔融体(金属或热渣)的输送(运输)是涉及安全、环境极为重要的生产工序,用于无轨输送(运输)的通道必须专门设置,且应避免与其他运输和人员交叉;线路设计应平缓、通畅确保安全,应符合相关标准规定;
12 在铜锍、镍硫水淬时,熔融的锍体与水发生剧烈反应,操作稍有不慎即会出现巨大地爆炸、喷溅,在某企业内已经出现过火灾等事故,应做好必要的防护;
13 采取各种措施减少静电、打火等火灾诱发因素;
14 有色金属部分稀有品种生产,其采用介质及工艺环节都具有较高的火灾危险性,例如钛的冶炼生产需经氯化还原,加镁粉还原蒸馏,以及真空蒸馏等一系列化工冶金过程,最终获得海绵钛产品。其生产工艺过程具有较高的火灾危险性,成品海绵钛则属于易燃、易爆品。当海绵钛发生燃烧并遇到适量的水时,立即产生氢气发生剧烈燃烧甚至发生爆炸。因此,在该类厂房中,不得使用水灭火并避免大量冲洗水。本条根据现行行业标准《钛冶炼厂工艺设计规范》YS 5033—2000第8.4节的有关规定制定。
4.5.6 冶炼生产厂房内具有熔融体作业区的防火设计应符合下列规定:
1 作业区范围内(含地下、上空)严禁设置车间生活间;
2 应采取防止雨雪飘淋室内的措施,严禁地面积水;不应在场地内设置水沟和给、排水管道,当必需设置时,应有避免水沟中积存水和防止渗漏的可靠构造措施;
3 作业区不宜设置各类电缆、可燃介质管线,当必需设置时,应采取可靠的隔热保护措施;
4 厂房的耐火等级不应低于二级,受到热作用的结构构件宜采取有效、合理的隔热防护,钢结构构件可按本规范附录A进行耐火稳定性验算或采取防火保护措施。
位于冶炼炉及其出渣、加料、浇铸等作业区周边及上方,具有高温熔融体强烈烘烤和大量火星剧烈喷溅,若遇水或易燃气体泄漏还将产生严重的爆炸。
1 在冶金生产实践中,熔融体作业区是火灾事故的高发区之一。因此,本区域严禁设置车间生活间,也不应设置主要的人行通道,无关的设施和人员应远离该区域。2007年4月18日发生在某特殊钢公司钢水包倾覆事故,30t重1000℃以上炽热的钢水顷刻涌入交接班室,造成了32人死亡、6人受伤的特重大事故。“4·18”惨案经深入调查认定原因是多方面的,其中深刻教训之一是:交接班室设置在距铸锭点仅5m的炉体下方的小屋内,疏散、扑救十分困难,致使正在交接开会的工人难以幸免,伤亡十分惨重!鉴于此,本规范以强制性条款明确规定:此区域严禁设置车间生活间;
2 做好冶炼厂房的防雨、排水等设计,尽可能不在熔融体作业区域设置管沟。如果设置了管沟,需要特别作好防止熔融体渗漏进管沟的措施;也要防止地下管沟可能积水,避免在高温的烘烤下积水快速汽化,体积急剧膨胀引起爆炸。类似的事故都曾经在有色企业发生过,应当汲取教训;
4 熔融体作业区域内各类生产操作喷溅严重,辐射热很高,对周边厂房结构产生的热作用较强,宜对梁、柱设置隔热防护层。另外,鉴于发生过钢包磕碰厂房构件的事故,设计应留有足够的操作间隙和采取必要防护措施,防止碰撞避免引发火灾事故。
4.5.7 冶金炉窑的烟气处理、余热回收工艺的防火设计应符合下列规定:
1 各类工艺装置应选用不燃烧体或难燃烧体,并确保工艺装置的密闭性;
2 应有防止烟气收尘系统中的装置发生燃烧或爆炸的技术措施;
3 余热回收利用中的高压设施及其管线、阀门,应符合现行国家标准《钢制压力容器》GB 150和相关安全监督标准的有关规定。
将冶炼工艺产出的高温粉尘、烟气等予以回收,既净化了环境,又利用了资源。一般烟尘采用沉尘室、旋风器、滤袋、电收尘等干法以及水膜式、冲击式洗涤器、文秋里管等湿式收尘设施予以回收。对于产量大、温度高的烟气,通过设置余热锅炉系统,回收余热实现节能。之后并将含SO2的烟气送制酸工序生产硫酸,或经净化治理达标后的尾气排放。
1 以往某些冶炼炉收尘器的材料、构造上设计欠妥当,引起浓烟泄漏、火星飞溅等发生。甚至还出现过收尘器中的滤袋被点燃、烧毁等的事故,应当加以防止;
2 在鼓风炉等大、中型炉窑烘炉期间或间断运行时,因不完全燃烧会有多量的一氧化碳进入收尘器,从而引发起燃烧、爆炸事故,应采取技术措施加以防止;
3 余热回收利用装置(含余热锅炉、汽化冷却装置等)均系高温、高压体系,安全防护要求格外严格。90年代中期,西部某有色公司在冶炼余热锅炉试生产阶段,因系统中使用了压力、温度不匹配的配件,致使高温、高压蒸汽发生严重外泄,巨大且灼热气流击碎相邻的窗玻璃,直接袭击控制室,导致一死三伤和众多装备损坏的重大事故发生。
正文中提及的相关标准,还有《锅炉房设计规范》GB 50041、《压力容器安全技术监察规程》(质技监局锅发1999 154号)等有关规定。